A Warm Welcome to Our Newest Machine, the Full Spectrum PS36 Laser Cutter.
A brief history on laser cutting:
The first working laser cutter was created in the 1960s by Western Electric, one of the forerunners of laser technology in manufacturing. Manufacturers soon began using lasers in their processes to allow for much faster production. Many advances have been made since then, such as metal cutting and glass etching. Today, we see more affordable options, better software support, and small-sized machines made specifically for makers. It truly has never been easier to get started with laser cutting.
Our laser cutter operates using CNC or Computer Numerical Control. This allows us to draft our designs on a computer program such as Adobe Illustrator or AutoCAD and upload them to the machine similarly to how a printer works. Laser cutting is accurate — the narrow beam of high energy light on our machine is merely 0.002”, or 0.05 mm. This is what makes laser cutting so unique: high accuracy and fast cutting of certain materials. Traditional methods such as saws and blades are not as fast, quiet, or clean. CNC combined with the highly accurate laser allows for intricate designs or even photo etching automagically.
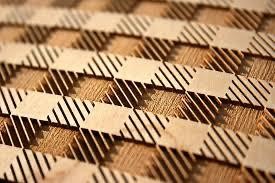
An example etching piece created on a laser.
Laser cutters are limited in the materials that are safe to use without an industrial filter system, but luckily this includes all types of wood, specific plastics, and most fabrics. Materials that are not safe are plastics such as PVC, vinyl, or ABS. These plastics are commonly used in manufacturing today, but release harmful chlorine gas or hydrochloric acid when burned. This is why, when working with plastics especially, it is important to know exactly what material you want to cut and if it is safe to use on a laser.
Hobbyists and makers have welcomed laser manufacturing with open arms, as they make an effective tool for a variety of uses. Wood burning and etching, carpentry, and other crafts can make use of the precisely controlled laser. Laser cutters are easy to use and setup, with very little clean up required. Makers unfamiliar with CNC can learn very easily through a laser with Adobe Illustrator or similar programs.
If you have any questions about laser cutting or want to get started, visit The Spark Makerspace in Willis library and talk to one of our skilled laser operators!
Written By: M. Heins